Exploring the World of Industrial Filtering Materials
Industrial filtration plays a crucial role in various industries, ensuring the quality and purity of liquids and gasses. The choice of filtering material is vital to achieving efficient filtration and meeting specific application requirements. In this article, we will explore the world of industrial filtering materials, discussing their types, applications, costs, and manufacturing process. As a trusted name in the industry, R.P.Fedder has been designing and manufacturing custom filters since 1959, providing tailored solutions to meet diverse filtration needs. Read on to discover the diverse range of filtering materials and understand why businesses should turn to R.P.Fedder for their custom filter requirements.
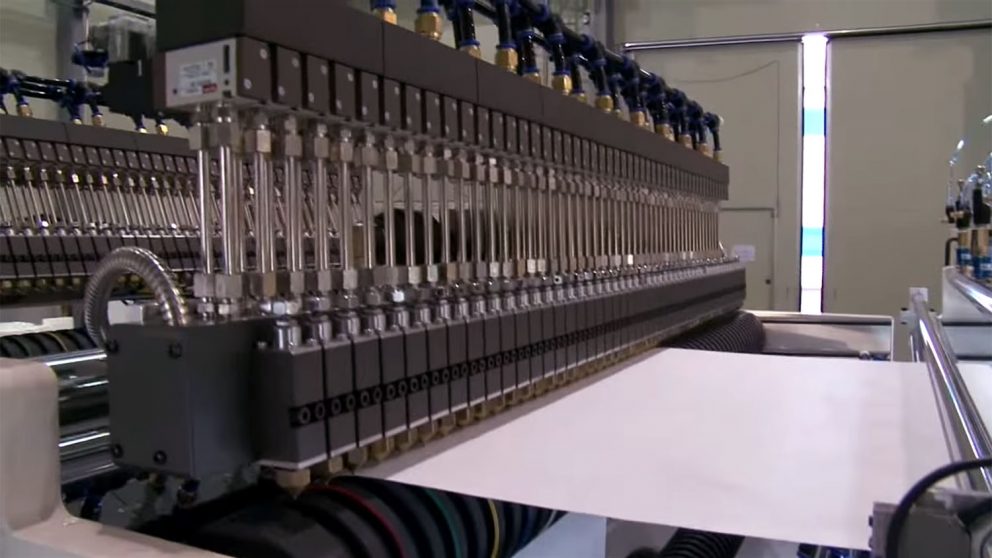
What Is Industrial Filtering?
Industrial filtering refers to the process of separating unwanted particles, contaminants, or impurities from liquids or gasses using specialized filters. These filters are designed to capture and retain particles while allowing the desired substance to pass through, resulting in improved quality, enhanced safety, and extended equipment lifespan. Industrial filtration finds applications across a wide range of industries, including manufacturing, automotive, pharmaceuticals, food and beverage, oil and gas, and many others.
What Are the Types of Industrial Filtration?
- Mechanical Filtration: This type of filtration relies on physical barriers to separate particles based on size. Common mechanical filters include screens, meshes, and membranes that trap contaminants larger than their pore size.
- Gravity Filtration: Gravity filtration employs gravity as the driving force to separate solids from liquids. It involves passing the liquid through a porous medium, such as sand or gravel, allowing the solids to settle out.
- Centrifugal Filtration: Centrifugal force is utilized in this type of filtration to separate particles from a fluid. The fluid is forced into a rapidly rotating cylindrical chamber, causing the denser particles to move towards the chamber wall and form a cake.
- Vacuum Filtration: Vacuum filtration employs negative pressure to draw the liquid through a filter medium, capturing the solids and leaving the clarified liquid behind. This method is commonly used in laboratories and industries where a high degree of separation is required.
- Pressure Filtration: Pressure filtration involves applying pressure to force the liquid through a filter medium. It is particularly useful in industries where a high flow rate is desired or when filtering viscous fluids.
- Electrostatic Filtration: Electrostatic filters employ an electrostatic charge to attract and capture particles. The charged filter medium attracts oppositely charged particles, enhancing filtration efficiency.
- Membrane Filtration: Membrane filtration uses a semipermeable membrane with tiny pores to separate particles based on their size. It is commonly used for removing bacteria, viruses, and other microscopic contaminants.
Common Materials Used in Industrial Filtering
Choosing the appropriate filtering material is crucial to achieving effective and efficient filtration. The selection depends on the specific application, desired filtration efficiency, chemical compatibility, temperature resistance, and other factors. Here are some common materials used in industrial filtering:
- Cellulose: Cellulose-based materials, such as paper, are widely used in industrial filtration due to their high efficiency in capturing solid particles. These materials are cost-effective and offer good compatibility with various fluids.
- Polypropylene: Polypropylene filters exhibit excellent chemical resistance and are commonly used in applications where aggressive chemicals are present. They are suitable for both liquid and air filtration.
- Activated Carbon: Activated carbon filters are highly effective in adsorbing organic compounds and removing odors. These filters find applications in air purification, water treatment, and gas-phase filtration.
- Metal Filters: Metal filters, typically made of stainless steel or aluminum, offer exceptional durability and can withstand high temperatures and harsh environments. They are commonly used in heavy-duty industrial applications.
- Polyester: Polyester filters are known for their high strength, chemical resistance, and excellent dimensional stability. They are suitable for applications involving high temperatures and corrosive fluids.
- Nylon: Nylon filters offer excellent tensile strength, chemical resistance, and dimensional stability. They are commonly used for filtering oils, fuels, and hydraulic fluids.
It’s important to note that the choice of filtering material depends on the specific requirements of the application. R.P.Fedder specializes in designing and manufacturing custom filters, offering a wide range of materials to meet unique filtration needs.
What Industries Use Filtration?
Industrial filtration is integral to numerous industries, including:
- Pharmaceuticals: Filtration is crucial in pharmaceutical manufacturing to ensure the removal of contaminants, bacteria, and particles, ensuring product purity and safety.
- Chemicals: Chemical production often involves separating impurities and by-products through filtration, ensuring product quality and compliance with industry standards.
- Food and Beverage: Filtration is essential in the food and beverage industry to remove impurities, clarify liquids, and maintain product consistency and safety.
- Automotive: Filtration is employed in the automotive industry for applications such as oil, fuel, and air filtration, ensuring optimal engine performance and longevity.
- Water Treatment: Water treatment facilities utilize filtration systems to remove sediments, chemicals, and microorganisms, ensuring clean and potable water for communities.
- Oil and Gas: The oil and gas industry relies on filtration to remove solids, water, and contaminants from crude oil, natural gas, and refined products. It helps protect equipment, ensure product quality, and maintain operational efficiency.
- Power Generation: Power plants employ filtration to purify water used in cooling systems, remove particulate matter from exhaust gasses, and protect critical equipment such as turbines and generators.
What Factors Affect the Cost of Industrial Filtration?
Several factors influence the cost of industrial filtration systems:
- Filtration System Design: The complexity of the filtration system design, including the required flow rate, pressure, and desired efficiency, impacts the overall cost. Customized solutions may involve higher upfront costs but offer long-term benefits.
- Filtering Material Selection: The choice of filtering material can significantly affect the cost. Some materials are more expensive than others due to their unique properties, availability, or manufacturing processes. Balancing cost with performance is crucial.
- Maintenance and Replacement: Regular maintenance and filter replacement are essential to ensure optimal filtration performance. Considering the ongoing costs associated with maintenance and replacement is vital for overall cost assessment.
- Volume and Frequency: The volume of fluid or gas to be filtered and the frequency of filtration can impact costs. Higher volumes and more frequent filtration may require larger or more advanced filtration systems, which can affect overall expenses.
- Operating Conditions: Factors such as temperature, pressure, chemical compatibility, and environmental conditions influence the selection of suitable filtering materials and can impact costs.
How Are Industrial Filters Manufactured?
At R.P.Fedder, we follow a meticulous manufacturing process to deliver high-quality industrial filters:
- Design and Specification: R.P.Fedder collaborates with clients to understand their filtration requirements and specifications. This step includes determining the filtration medium, size, shape, and desired performance characteristics.
- Material Selection: Based on the requirements, R.P.Fedder selects the appropriate filtering material, considering factors such as chemical compatibility, temperature resistance, and filtration efficiency.
- Cutting and Shaping: The selected filtering material is cut and shaped according to the desired specifications using advanced cutting techniques and machinery.
- Assembly: The components of the filter, including frames, supports, seals, and filter media, are assembled meticulously to ensure a secure and reliable filtration system.
- Quality Control: Rigorous quality control measures are implemented at every stage of the manufacturing process to ensure that the filters meet the highest standards and comply with client specifications.
- Testing and Validation: The manufactured filters undergo rigorous testing to verify their performance, efficiency, and durability. This ensures that the filters are ready for deployment and deliver the desired results.
What Is the Best Material for a Filter?
The choice of filtering material depends on various factors such as the application, operating conditions, desired filtration efficiency, and budgetary considerations. At R.P.Fedder, our team of filtration experts can guide you in selecting the most suitable material based on your specific needs. We offer a diverse range of filtering materials, including cellulose, polypropylene, activated carbon, metal filters, and polyester, ensuring that we can design and manufacture filters tailored to your unique requirements.
Why Choose R.P.Fedder?
For over six decades, R.P.Fedder has been a trusted name in the industry, offering comprehensive solutions for custom filter design and manufacturing. Here’s why businesses should choose us:
- Experience and Expertise: With a rich history dating back to 1959, we possess extensive knowledge and expertise in filtration systems across various industries.
- Customization: We understand that every filtration requirement is unique. Our team excels in developing tailored solutions that precisely meet your specifications, ensuring optimal filtration performance.
- Quality Assurance: We adhere to stringent quality control measures throughout the manufacturing process to deliver filters that consistently meet or exceed industry standards.
- Cost-effectiveness: Our filters are designed with longevity and efficiency in mind, providing cost-effective solutions that deliver long-term value for your business.
- Technical Support: We offer comprehensive technical support and after-sales service to ensure your filtration system operates at its best, providing ongoing assistance whenever needed.
Industrial filtering materials play a critical role in maintaining product quality, process efficiency, and a safe working environment across various industries. Understanding the different types of filtering materials and their applications is key to selecting the optimal solution for your filtration needs. R.P.Fedder, with its decades of experience and expertise, stands ready to design and manufacture custom filters that meet your specific requirements. Contact us today to discover how our tailored filtration solutions can elevate your operations to new heights.