Industrial Filtration Process: Why It’s Important and Its Uses
Industrial filtration is the process of removing contaminants from air and other gases in a manufacturing or industrial setting. By removing these particles, industrial filtration helps to protect equipment and the work environment. In this comprehensive guide, we will explore everything you need to know about industrial filtration. We’ll start by discussing what industrial filtration is and the step-by-step industrial filtration process. Then we’ll take a look at the different types of industrial filtration and filters, why industrial filtration is important for industries ranging from pharmaceuticals to power generation, and the uses of industrial filtration systems. By understanding industrial filtration systems and the different types of industrial filters available, you can make informed decisions when selecting an industrial filtration system.
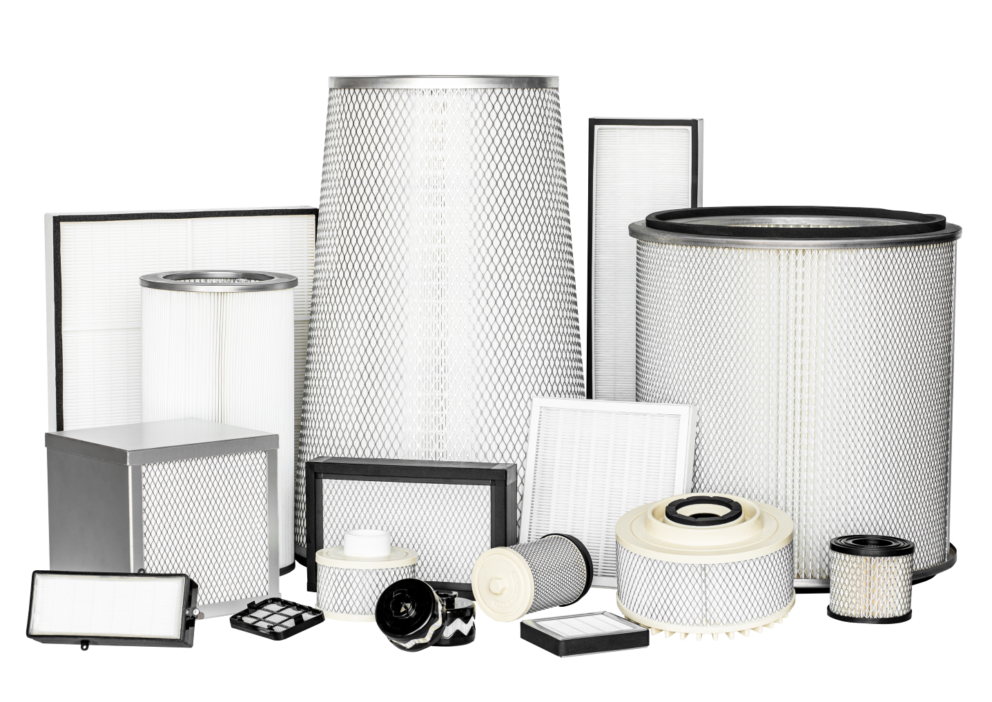
Industrial filtration process
The industrial filtration process begins with the selection of appropriate industrial filters. Depending on the specific application, industrial filters can be chosen from a range of different types. These include:
- Mechanical filters: These filters use mechanical means to strain large particles from the air or gas.
- Absorptive filters: These industrial filters absorb small particles, gases, and vapors using chemical sorbents.
- Activated carbon filters: These industrial filters use activated carbon to remove odors, gases, and other contaminants from air or gas.
- Electrostatic precipitators: These industrial filters use charged particles to attract and capture dust, smoke, and other airborne contaminants.
- Chemical filters: These industrial filters use chemical reactions to remove contaminants from air or gas.
- Biological filters: These industrial filters use bacteria or other microorganisms to remove contaminants from air or gas.
- Membrane filters: These industrial filters use a membrane to remove particles, dissolved solids, and other contaminants from air or gas.
- EMI/RFI filters: These industrial filters use an electromagnetic field to reduce the interference or radiation of electronic devices.
- Electronic filters: These industrial filters use an electronic circuit to reduce noise and other undesired signals from the air or gas.
- Fluid filters: These industrial filters use fluids to reduce particulate contaminants in a gas or liquid.
- Hydraulic filters: These industrial filters use a system of valves, pumps, and other components to reduce contaminants in a liquid.
- Cyclone filters: These industrial filters use centrifugal force to separate particles from the air or gas.
- Gravity filtration: These industrial filters use gravity to remove particles from the air or gas.
- Vacuum filters: These industrial filters use a vacuum to remove particulates and other contaminants from air or gas.
- Cold filters: These industrial filters use a cold temperature to remove airborne contaminants from the air or gas.
- Hot filters: These industrial filters use a hot temperature to remove airborne contaminants from the air or gas.
Once the industrial filter has been selected, it must be properly installed in order for industrial filtration to take place. Proper installation of industrial filters typically involves connecting them to a source of air or gas flow, such as a blower or industrial compressor. The industrial filter should then be tested to ensure that it is working correctly and meeting the desired specifications.
Once industrial filtration begins, airborne contaminants are captured by the industrial filter media and collected in a filter element or other containment device. Depending on the type of industrial filter used, this may involve either filtering out particulate matter, capturing chemicals and gases, or using a combination of both.
Industrial filtration systems must be regularly serviced and maintained in order to ensure that they are operating properly. Regular maintenance of industrial filters will help to keep your industrial environment safe and efficient by preventing the buildup of air pollutants over time.
Depending on the type of industrial filter used, the industrial filtration process may involve one or several steps:
- Pre-Filtering: In some cases, such as with industrial hydraulic filters, a pre-filter is used to separate large particles and other contaminants from the air or gas.
- Filtration: The industrial filter is then placed in the industrial system to capture smaller particles, gases, and other contaminants. Depending on the type of industrial filter used, this process may involve mechanical filtration, absorptive filtration, electrostatic filtration, or chemical filtration.
- Post-Filtering: In some industrial systems, a post-filter is used to capture any particles missed by the industrial filter. This step may involve biological filters, membrane filters, EMI/RFI filters, electronic filters, fluid filters, or hydraulic filters.
Once the industrial filtration process is complete, the industrial filter can be removed and disposed of properly.
Why industrial filtration is important
Industrial filtration is an essential part of industrial operations because it helps to protect the environment from air pollution. Industrial filters can be used to capture particulate matter such as dust, smoke and fumes that can put workers at risk for health problems.
Other reasons industrial filtration is critical:
- Productivity: Industrial filtration helps to reduce downtime and keep industrial equipment functioning properly.
- Safety: Industrial filtration reduces the risk of industrial accidents by trapping hazardous particles in industrial filters before they can enter the work environment.
- Cost Reduction: Industrial filtration can help industrial facilities save money by reducing energy costs, increasing the life of industrial equipment and preventing costly industrial accidents.
- Recycling: Industrial filtration can help industrial facilities reduce the amount of waste that is generated, saving money and helping to conserve resources.
- Systematic waste disposal: Industrial filtration can help industrial facilities manage the disposal of industrial waste in a safe and efficient manner.
- Energy consumption: Industrial filtration systems help to reduce energy consumption by filtering out contaminants, which can improve industrial productivity.
Uses of industrial filtration
Industrial filtration can be used in a variety of industrial applications including pharmaceutical and food processing, power generation, healthcare, refining, and manufacturing. Industrial filters are an essential part of industrial operations as they help protect equipment and workers from contaminants in the air or gas.
Common industrial filtration applications include:
- Dust collection: Industrial filters are used to capture dust and particulate matter from industrial processes such as grinding, welding, and machining.
- HVAC systems: Industrial filters can be used to remove allergens, pollutants, and other airborne contaminants from heating, ventilation and air conditioning systems.
- Gas turbine protection: Industrial filters are used to protect gas turbines by filtering out particles that could damage the turbine blades.
- Water filtration: Industrial filters can be used to filter out suspended solids, chemicals, and other contaminants from industrial water systems.
Factors to consider when choosing industrial filtration system
Choosing the right industrial filtration system is important in order to ensure that it meets the needs of your industrial operation. When selecting an industrial filter, you should consider factors such as:
- Type of contaminants: Different industrial filters are designed to capture different types of contaminants. For example, industrial hydraulic filters are used to capture large particles, while industrial air filters can be used to capture smaller particles and gases.
- Flow rate: The industrial filter should have a flow rate that is suitable for your industrial operation.
- Air pressure: The industrial filter should be able to maintain the necessary air pressure for your industrial system.
- Pressure drop: Related to flow rate and air pressure, the industrial filter should be able to handle the pressure of your industrial system. Pressure drop refers to the measurement of resistance to air that passes through the filter.
- Size: The industrial filter should be the right size to fit in your industrial system.
- Environmental conditions: The industrial filter should be able to withstand the environmental conditions of your industrial system.
- Maintenance: Some industrial filters require more frequent maintenance than others. It’s important to select an industrial filter that is easy to maintain and service regularly in order to ensure optimal performance.
- Safety regulations and standards: Industrial filters should be able to meet safety regulations and standards in order to protect workers.
- Available space: The industrial filter should be able to fit into the space available in your industrial system.
- Cost: Industrial filters can vary in cost depending on the type and size. It’s important to select an industrial filtration system that fits within your budget.
The best industrial filtration process will depend on the specific needs of your industrial system. It’s important to consider all the factors outlined above when selecting an industrial filtration system in order to ensure optimal performance and safety.
Contact R.P. Fedder’s experienced team today
Industrial filtration is an essential part of industrial operations as it helps to protect equipment and workers from contaminants in the air or gas. By understanding what industrial filtration is, the industrial filtration process, industrial filter types, uses of industrial filters, and factors to consider when choosing industrial filters, you can ensure that your industrial operation is equipped with the best industrial filtration system for its needs. By considering all of these factors, you can ensure that your industrial operation is secure and productive.
To learn more or if you have questions, contact the experts at R.P. Fedder. Our experienced team of industrial filtration professionals is here to help you select the industrial filter that best suits your industrial needs. Get started on finding the industrial filtration system that fits your industrial operation’s needs.