Types of Industrial Filtration and Their Applications
Industrial filtration plays a crucial role in various industries, ensuring the removal of impurities and contaminants from fluids and gasses. Effective filtration is essential for maintaining product quality, equipment longevity, and overall operational efficiency. We will explore the different types of industrial filtration, their applications, the components involved, and the factors that affect the cost. As an industry leader in designing and manufacturing custom filters since 1959, R.P. Fedder has the expertise to provide tailored solutions that meet the specific filtration needs of businesses. Let’s delve into the world of industrial filtration and discover the diverse range of filtration types and their applications.
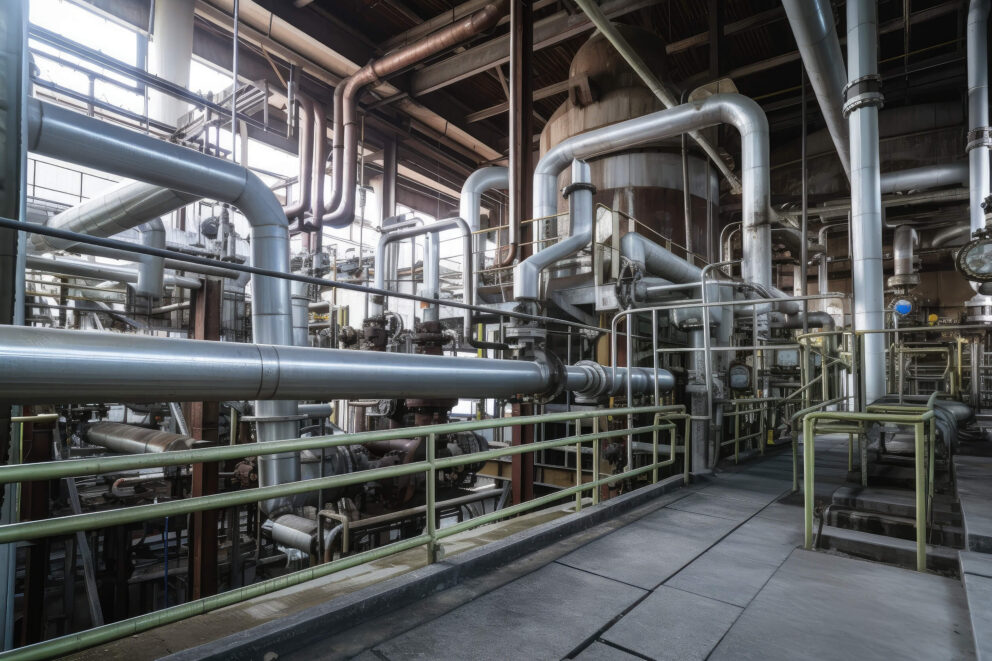
How Does the Process of Industrial Filtration Work?
Industrial filtration is a process that involves separating unwanted particles or contaminants from a fluid or gas stream. The filtration process typically consists of the following steps:
- Filtration Medium Selection: Depending on the specific application and desired level of filtration, the appropriate filtration medium is selected. It could be a porous material, a depth filter, or a membrane.
- Filtration Mechanisms: Filtration can occur through various mechanisms such as mechanical screening, straining, adsorption, absorption, and electrostatic attraction. The choice of mechanism depends on the nature and size of particles to be removed.
- Filtration Equipment: Industrial filtration systems employ a wide range of equipment, including filter presses, cartridge filters, bag filters, centrifuges, and more. These systems are designed to facilitate the separation process efficiently.
- Filtration Process: The fluid or gas to be filtered is passed through the chosen filtration medium, which traps and retains the unwanted particles while allowing the clean fluid or gas to pass through.
- Maintenance and Cleaning: Regular maintenance and cleaning of the filtration system are essential to ensure optimal performance and longevity. This may involve replacing filter media, cleaning clogged filters, and monitoring pressure differentials.
What Is the Main Purpose of Filtration?
The primary purpose of industrial filtration is to remove contaminants, impurities, or unwanted particles from fluids and gasses. This process serves several vital purposes:
- Quality Control: Filtration ensures that the final product meets the desired quality standards by eliminating particles that could affect its appearance, taste, texture, or performance.
- Equipment Protection: Filtering out contaminants prevents the accumulation of debris, sediment, or corrosive substances in equipment or machinery, extending their lifespan and reducing maintenance costs.
- Environmental Compliance: Filtration plays a critical role in meeting environmental regulations by removing pollutants or harmful substances from industrial processes before their discharge.
- Process Efficiency: Effective filtration enhances process efficiency by minimizing downtime caused by equipment failures, reducing the need for frequent cleaning or replacement, and optimizing overall system performance.
What Are the Types of Industrial Filtration?
Industrial filtration encompasses various types, each designed to address specific filtration requirements. The main types of industrial filtration include:
- Mechanical Filtration: This type of filtration relies on physical barriers to trap and remove particles. It is commonly used for coarse filtration, where larger contaminants need to be removed. Examples include screens, sieves, and strainers.
- Depth Filtration: Depth filters consist of porous materials, such as fibrous media, which trap particles within their structure as the fluid flows through. They are effective for removing contaminants of various sizes and are widely used in industries like pharmaceuticals, food and beverage, and water treatment.
- Membrane Filtration: Membrane filters feature a thin, semi-permeable membrane with pores of specific sizes. They allow the passage of particles smaller than the pore size while blocking larger particles. Membrane filtration is used for precise separation and is crucial in applications such as pharmaceutical manufacturing, biotechnology, and electronics.
- Adsorption Filtration: Adsorption filters use adsorbents, such as activated carbon, to attract and retain contaminants. They are particularly effective in removing dissolved impurities, organic compounds, and odors. Adsorption filters find applications in water purification, air treatment, and gas processing.
- Electrostatic Filtration: This type of filtration utilizes the electrostatic attraction between charged particles and a collection surface. Electrostatic filters are commonly used in industrial settings to remove fine particulate matter from gasses, such as in HVAC systems, power plants, and cleanrooms.
What Are the Applications of Industrial Filtration?
Industrial filtration has widespread applications across various industries. Some notable applications include:
- Oil and Gas: Filtration is essential in oil refineries, natural gas processing plants, and petrochemical industries to remove impurities from crude oil, gas streams, and process fluids.
- Water Treatment: Filtration plays a vital role in treating both drinking water and wastewater. It removes suspended solids, bacteria, viruses, and other contaminants to ensure clean and safe water.
- Pharmaceuticals and Biotechnology: The pharmaceutical industry relies on filtration to ensure product sterility, remove particulates from drug formulations, and facilitate the purification of biopharmaceuticals.
- Food and Beverage: Filtration is crucial in the food and beverage industry for clarification, purification, and sterilization processes. It helps remove particles, sediments, and microorganisms, ensuring product quality and extending shelf life.
- Chemical Processing: Filtration is employed in chemical processing to purify raw materials, recover valuable substances, remove impurities, and control the quality of the final products.
- Automotive and Manufacturing: Industrial filtration is used to maintain the cleanliness of hydraulic fluids, lubricants, and cooling systems in automotive and manufacturing processes, preventing equipment damage and maintaining product quality.
- Electronics and Semiconductors: Filtration is vital in the electronics industry to achieve the high purity levels required for microchip manufacturing and other electronic component production processes.
What Are the Components of the Filtration Process?
Industrial filtration involves several key components working together to achieve effective separation. These components include:
- Filter Media: The filter media is the material through which the fluid or gas passes, trapping and retaining particles. It can be made of various materials like paper, cloth, metal, activated carbon, ceramic, or synthetic fibers, depending on the application.
- Filter Housing: The filter housing encloses and supports the filter media, ensuring proper alignment and sealing to prevent bypass. It also provides a connection for the inlet and outlet of the fluid or gas.
- Pressure Differential Indicator: This component monitors the pressure drop across the filter and indicates when it reaches a certain threshold, signaling the need for maintenance or filter replacement.
- Seals and Gaskets: Seals and gaskets ensure a secure and leak-free connection between the filter housing and other system components, preventing bypass and maintaining filtration efficiency.
- Supporting Structure: Larger industrial filtration systems often require a supporting structure to hold the filters in place and provide stability during operation. This structure may include frames, racks, or mounting brackets.
Common Materials Used in Industrial Filtering:
The choice of filtering materials depends on the specific filtration requirements and the nature of the particles to be removed. Some commonly used materials in industrial filtering include:
- Cellulose: Cellulose-based filter media offer excellent particle retention and are widely used in applications requiring high dirt-holding capacity. They are cost-effective and suitable for various filtration processes.
- Polypropylene: Polypropylene filters are resistant to chemicals and are commonly used in industries where high chemical compatibility is required. They are effective in removing sediments, particulates, and other contaminants.
- Activated Carbon: Activated carbon is a highly porous material with a large surface area, making it ideal for adsorption filtration. It is commonly used to remove odors, tastes, organic compounds, and certain chemicals from liquids and gasses.
- Fiberglass: Fiberglass filters offer high temperature resistance and are suitable for applications involving high operating temperatures. They are commonly used in industrial processes that require reliable filtration under extreme conditions.
- Stainless Steel: Stainless steel filters provide durability and corrosion resistance, making them suitable for harsh environments and applications involving high-pressure fluids or corrosive substances.
What Do the Different Filtering Materials Cost?
The cost of filtering materials can vary depending on factors such as material type, size, quality, and quantity required. Generally, synthetic materials like polypropylene are more affordable compared to specialty materials like activated carbon or stainless steel. However, the cost of filtering materials should be considered alongside their performance and suitability for the specific application.
What Factors Affect the Cost of Industrial Filtration?
Several factors influence the cost of industrial filtration systems. These include:
- Filtration Capacity: The required flow rate or volume of fluid/gas to be filtered affects the size and complexity of the filtration system, thereby influencing the cost.
- Filtration Precision: The desired level of filtration, whether it’s coarse, medium, or fine, affects the selection of equipment and filter media, which can impact the overall cost.
- Operating Conditions: Harsh operating conditions, high temperatures, corrosive environments, or the presence of hazardous substances may require specialized materials and construction, contributing to increased costs.
- Customization and Compliance: If the filtration system needs to be customized to meet specific requirements or comply with industry regulations, additional engineering and design work may be necessary, impacting the cost.
- Maintenance and Replacement: The frequency and cost of filter media replacement, cleaning, and system maintenance should be considered as part of the overall cost of filtration.
Why Should Businesses Contact R.P. Fedder?
Since 1959, R.P. Fedder has been a trusted industry leader in designing and manufacturing custom filters. Here are several reasons why businesses should consider partnering with R.P. Fedder for their filtration needs:
- Extensive Experience: With over six decades of experience, R.P. Fedder has developed deep expertise in filtration solutions across various industries. They understand the unique challenges and requirements of each industry and can provide tailored solutions that meet specific filtration needs.
- Customized Solutions: R.P. Fedder specializes in designing and manufacturing custom filters, ensuring that each solution is precisely engineered to address the client’s unique requirements. Their team of experts works closely with clients to understand their filtration goals and develop innovative, efficient, and cost-effective solutions.
- Quality and Reliability: R.P. Fedder is committed to delivering high-quality products that meet the most stringent industry standards. Their filters are built to withstand challenging operating conditions, ensuring long-lasting performance and reliability.
- Technical Support: R.P. Fedder provides comprehensive technical support throughout the entire filtration process, from initial design and engineering to installation and maintenance. Their experienced team is available to assist with troubleshooting, system optimization, and filter media selection.
- Cost-Effectiveness: By leveraging their industry knowledge and expertise, R.P. Fedder helps businesses optimize their filtration processes, minimizing downtime, reducing maintenance costs, and maximizing overall operational efficiency.
Industrial filtration is a vital process across a wide range of industries, ensuring the removal of contaminants and impurities from fluids and gasses. With its diverse range of filtration types, each tailored to specific applications, industrial filtration plays a crucial role in maintaining product quality, equipment longevity, and operational efficiency. R.P. Fedder, a trusted name in the industry since 1959, offers customized solutions and extensive expertise in designing and manufacturing custom filters. By partnering with R.P. Fedder, businesses can ensure efficient, reliable, and cost-effective filtration solutions that meet their unique requirements. Click here to learn more about our custom industrial filtration capabilities.